While the demand for logistics services continues to increase annually, today’s warehouse managers often struggle to meet this demand due to warehouse labor shortages. Warehouse labor shortages are a complex issue, with factors like increased market demand and high employee turnover playing roles.
Discover the causes of these warehouse labor shortages below, and learn nine inventive ways to attract workers to your warehouse.
Why are there warehouse labor shortages?
In some industries, warehouses may struggle to retain or recruit the staff required to meet the increased demand. For example, despite inflation and US tariffs, demand for e-commerce remains strong. The global e-commerce market was worth $25.9 trillion in 2023, and Grand View Research estimates that the e-commerce market will grow from 16.4% to 18.9% by 2030.
The transportation industry often struggles to attract and retain employees. Therefore, warehousing has one of the highest turnover rates among all sectors, averaging 49% in 2024. For instance, some companies report even higher rates, with Amazon reaching a 110% turnover rate during the pandemic.
Some of the factors that may play a role in warehouse employee turnover include:
- Aging workforce. The median age of a warehouse and transportation employee is 43, with 45% of all employees aged between 45 and 65+. When older employees retire, their absences often leave vacancies that are not appealing to younger generations.
- Lack of career paths Warehouse employees often feel limited by their opportunities for career advancement, with many positions offering no clear pathway forward. Across all industries, a lack of advancement opportunities was the second most common reason for quitting a job in 2021.
- Physical work. Warehouse jobs are often physically demanding. For example, an Amazon brochure notes that warehouse employees usually walk up to 13 miles or lift a combined 20,000 pounds in a single shift.
- Injury risk. The transportation and warehousing sector had the highest rates of work-related injuries and illnesses of all sectors in 2022, with an average of 3.8 per 100 workers. The injury rate rose by 20% between 2018 and 2022.
- Pay threshold. In 2025, the average annual salary of a warehouse worker is just under $34,000, or around $16 per hour for a 40-hour workweek. Combined with unclear career advancement paths, this might lead employees to consider higher-paying positions or roles with a more concrete path to higher earnings.
- Seasonal fluctuations. Finally, some warehouse positions are only available on a temporary basis, particularly during the holiday season, ranging from October to December.
Regardless of the reasons behind a high turnover rate, hiring new employees can be expensive for warehouse companies. For example, some industry professionals estimate that a single warehouse employee turnover can cost as much as $18,600 through a combination of lost productivity, new employee training, and other hiring expenses.
How to fight warehouse labor shortages
While staffing a warehouse may seem daunting, there are ways to attract new staff and retain existing personnel, such as improving employee engagement.
Workers who feel engaged at their jobs are more likely to stay in their positions and be more productive. According to Gallup, employee engagement can be increased by offering clear expectations, encouragement from management, and recognition of an employee’s contributions.
With that in mind, ways to improve employee engagement, attract a strong workforce to your warehouse, or meet productivity goals include the following.
Offer flexible arrangements.
According to Instawork’s 2024 State of Warehouse Labor report, flexible scheduling was the second most important incentive for attracting and retaining workers. Therefore, consider allowing employees to self-schedule shifts or more flexible shift selection options to accommodate employee preferences. For example, offer choices of eight or 10-hour shifts and weekend shifts.
Create advancement paths.
Give your workers an incentive to stay by designing a clear path toward career advancement in warehouse positions. For instance, employees who start by driving forklifts can work their way up to team leads, supervisors, or managers. When employees see a concrete future at your company, they are more likely to stay.
Implement a new WMS.
A warehouse management system (WMS) can do more than just keep your warehouse space organized – it also makes it easier for employees to do their jobs. For instance, one warehouse case study found that adopting a new WMS software available on iPads improved employee happiness and efficiency. Employees could access necessary information faster, making it easier for them to do their jobs. Sales increased by 50%, allowing the warehouse to expand by 25%.
Embrace warehouse automation trends.
Using warehouse robots can increase productivity while reducing the physical demands for employees. For example, automated sorting systems or picker robots can eliminate the need for employees to physically walk the warehouse. This can allow workers to remain in a more centralized location and avoid marathon-style walks over swaths of hard concrete.
Invest in warehouse training to combat warehouse labor shortages
Analyze the skills and specialties that account for the majority of your needs, such as managing automated equipment, and develop a warehouse training program to advance employees. Therefore, employees feel more engaged when they can learn and grow, and your warehouse can gain a staff with a broader skill set.
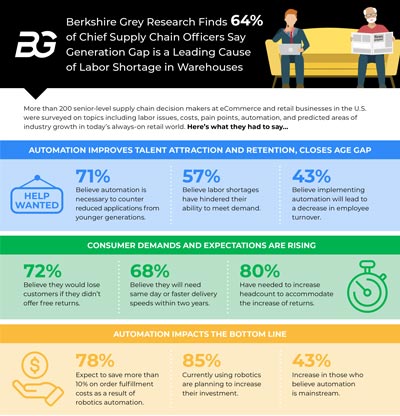
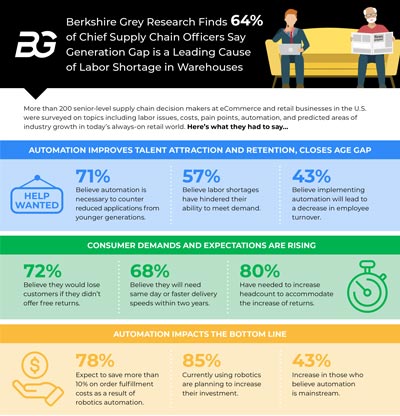
Improve warehouse safety
Although it may seem like a given, it is essential to consistently create a culture of safety and adhere to OSHA guidelines to protect employees. For instance, Ideas to improve warehouse safety include conducting regular risk assessments and offering ongoing training sessions on proper physical lifting and forklift practices.
Providing clear feedback can help warehouse labor shortages
Employees feel more satisfied at work when they feel appreciated. Therefore, invest in management personnel who can provide personalized feedback to employees, alongside encouragement for a job well done. For instance, even a single one-on-one conversation with a manager can improve employee engagement.
Offer incentives to prevent warehouse labor shortages
Consider offering your employees a reason to succeed with a pay-for-performance model. For instance, offer a bonus when they meet a set productivity target, provided it can be achieved safely without compromising on warehouse safety measures or cutting corners.
Immediate, short-term rewards are typically preferable, such as gift cards or a cash bonus. However, you could also take things a step further by offering your employees a referral bonus for attracting friends or family to your warehouse job openings.
Ensure employees understand their roles.
While understanding your role in an organization may seem basic, a survey from the London School of Commerce found that over 60% of warehouse employees didn’t understand employer expectations or know how their performance would be measured.
Ensure you communicate your expectations with employees clearly, so they can understand where to concentrate and focus on delivering a job well done.
A Rhode Island Warehouse for the Future
N&D Transportation prides itself on exceeding our logistics clients’ expectations and providing a safe, sustainable workplace for our employees. Additionally, we offer direct distribution services throughout the New England area from our centrally located Rhode Island warehouse and nationally through our carrier partners.
Learn more about how we can help your business grow by contacting us online or by calling (401)762-3337.