Running a warehouse is a complicated task, especially if you’re new to the business. Many first-time warehouse owner-operators can run into common warehouse problems that can impact your productivity, staff safety, and overall bottom line. But we’re here to help you find the solutions
Below, you’ll find a list of 10 common warehouse problems that can throw your operations off-track, along with ideas for improvement. Plus, discover a Rhode Island warehouse ready to fulfill all your storage needs.
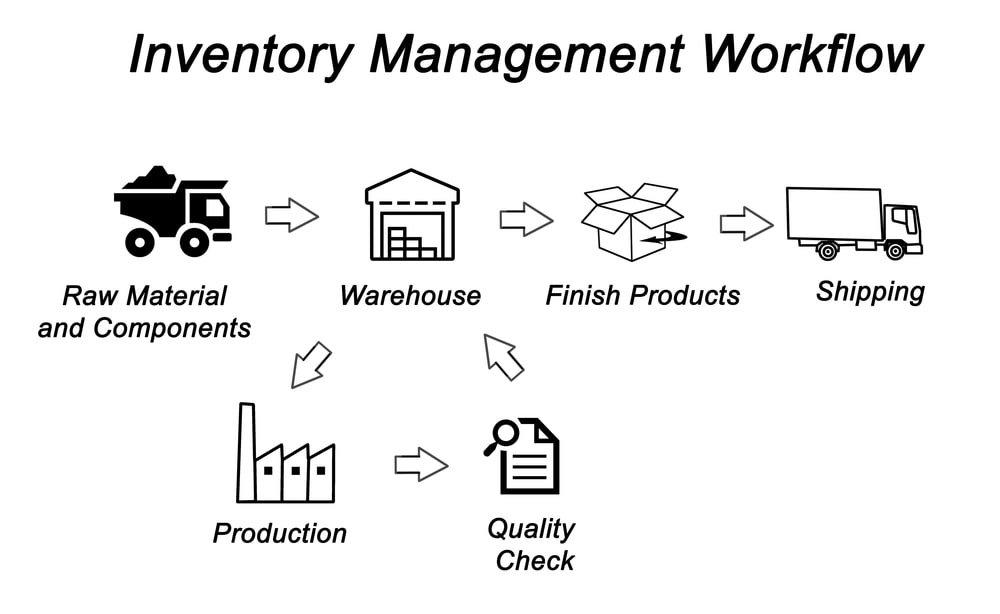
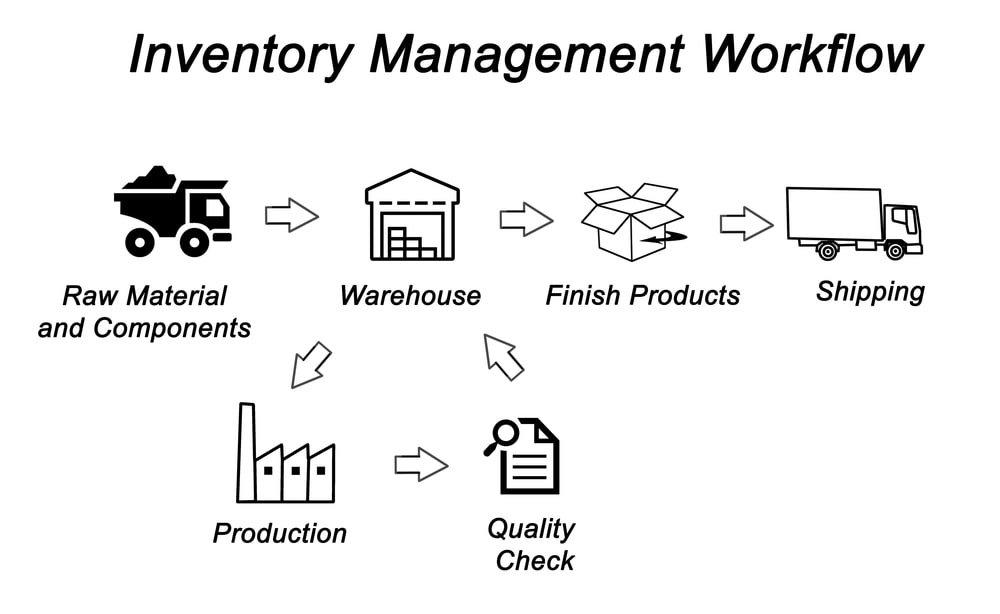
Using an unoptimized warehouse layout
You may have enough space for all of your inventory. But, an unorganized warehouse can lead to bottlenecks, delays, and even higher chances of collisions.
To optimize your warehouse layout, consider what products are most in demand. These items should be closer to your packing areas, so they can ship out faster. You can also improve your layout by implementing common warehouse layout types, such as shelves arranged in U, I, and L shapes.
Not having a warehouse management system
While smaller operations may get by with a spreadsheet system like QuickBooks, a larger warehouse needs a warehouse operation system (WMS) to stay efficient.
WMS is software that keeps track of every piece of your inventory. By incorporating this system into your warehouse, you can minimize delays and lost items, and you’ll always know exactly where everything is at all times.
Common warehouse problems – Understocking and overstocking
Understocking popular items can result in shipping delays or lost profits. At the same time, overstocking can take up valuable storage space and leave you without enough room for more important items.
But another perk of using WMS is its ability to track inventory trends over time. This can help you understand which items are most in demand, allowing you to keep the right amount in stock at all times.
Not having safety measures in place
Following less-than-optimal procedures or storing items in unideal areas can also increase the risk of workplace injuries for staff. For example, placing heavy items on higher shelves can lead to overexertion sprains to the back and shoulders. Instead, place heavy items on lower shelves, to minimize the risk of potential injuries.
Placing outbound and receiving loading areas in the same space
While you may think that combining your outbound and inbound loading docks will save space, it can actually cause more confusion. Your staff may accidentally ship out palettes meant to go in storage or put a priority order back on the shelves.
Instead, save yourself the potential headache by separating outbound and inbound loading docks.
Not embracing new technology can lead to common warehouse problems
The logistics industry is one of the most fast-paced on the planet. So, you can’t afford to keep your equipment and technology stuck in the past.
Keep up with warehousing technology trends, like automated picking tools or conveyor belt sorting racks. These new additions can free up staff in your warehouse to focus on other tasks, allowing you to increase productivity.
Neglecting maintenance can cause common warehouse problems
It’s not enough just to buy the necessary equipment. You also need to ensure it undergoes regular maintenance and inspections. For example, it’s a good idea to service a forklift every 250 to 300 hours. But you may need to service yours more often, especially if they are used frequently or operated in a hot or cold climate.
Remember to implement maintenance and service for all your equipment when building a schedule for your warehouse. It could help you save money by avoiding the cost of fixing a broken piece of equipment and keep your staff safe.
Under-training staff
A lack of warehouse training can leave your staff unprepared to perform their jobs efficiently and safely. So, invest in warehouse safety training sessions and educational resources to increase awareness.
For instance, train your staff to follow a lock-out, tag-out policy to keep equipment from accidentally turning on. Or, provide resources on proper lifting techniques to prevent neck or back injuries when moving heavy objects.
Falling behind on housekeeping
A warehouse needs regular cleaning, just like any other space. Dust and dirt in the air can create breathing and air quality issues, and discarded items in the aisles can present a tripping hazard.
To remedy these issues, organize a regular cleaning schedule for your warehouse. Anything you no longer need should go into the trash, and you can eliminate dust and particles through filter systems or shop vacs. You can make lasting strides toward a cleaner and safer facility by implementing these small steps.
Failing to plan for growth
Your business needs today may not accurately reflect your needs five years from now. But if you become too committed to a single process, warehouse layout, or software, you can risk falling behind your competitors.
Take some time every year to assess your current needs and how they’ve changed from previous years. What changes in your warehouse strategy can you make to adapt for the future? Maybe you can consider adding a movable mezzanine to take advantage of your vertical space or upgrading to a WMS with a barcode scanning system.
You may even find it more cost-effective and efficient to outsource your warehousing needs to a third-party warehousing provider.
Choose a Rhode Island warehouse to alleviate common warehouse problems
Running a warehouse on your own can be a daunting task. So, if you’re considering outsourcing to a New England warehouse, N&D Transportation Company Inc is up for the task.
Our 12-acre North Smithfield facility has a distribution warehouse full of racked, heated, and secure storage space. Rent out as much or as little space as you need, for as long as you want. We can also help you distribute directly throughout the New England area, so you won’t need to work with another shipping provider.
Contact us today to learn more about how we can fulfill your storage needs.