Nobody likes a late package, but in some cases, shipping delays are unavoidable. The worldwide freight industry is heavily intertwined with current events, as the wave of delays and backlogs from the COVID-19 pandemic proved. But even when a global pandemic isn’t at play, a crisis in one part of the planet can still have ripple effects throughout the global supply chain.
While you can’t always control shortages or transportation delays, you can help your business develop supply chain resilience to prevent business interruptions or bounce back afterward. Below, learn more about what causes supply chain interruptions and find six strategies to keep your logistics operations running smoothly.
What causes shipping delays?
Some of the most common causes of 2024 supply chain disruptions post-2020 include the following.
- Geopolitical conflict. Russia’s invasion of Ukraine disrupted shipping operations in the black sea, which connects trade routes between Europe and Asia.
- Blocked trade routes. Some trade routes may be blocked due to other causes, like when the Evergiven container ship became stuck in the Suez Canal.
- Port backlogs. COVID triggered a buildup of port backlogs on both the west and east coast, which have endured even years after restrictions were lifted.
- Shipping container shortages. Production of shipping containers dipped during the pandemic, causing shortages and price increases.
- Bad weather. Storms, like hurricanes, typhoons, and blizzards, may impact your supply chain through weather delays.
- Labor shortages & strikes. The 2024 port workers’ strike led to port congestion and a buildup of unloaded shipping containers.
- Material shortages. Sometimes, a shortage of materials or raw goods could impact production. For example, copper is in short supply as of 2024.
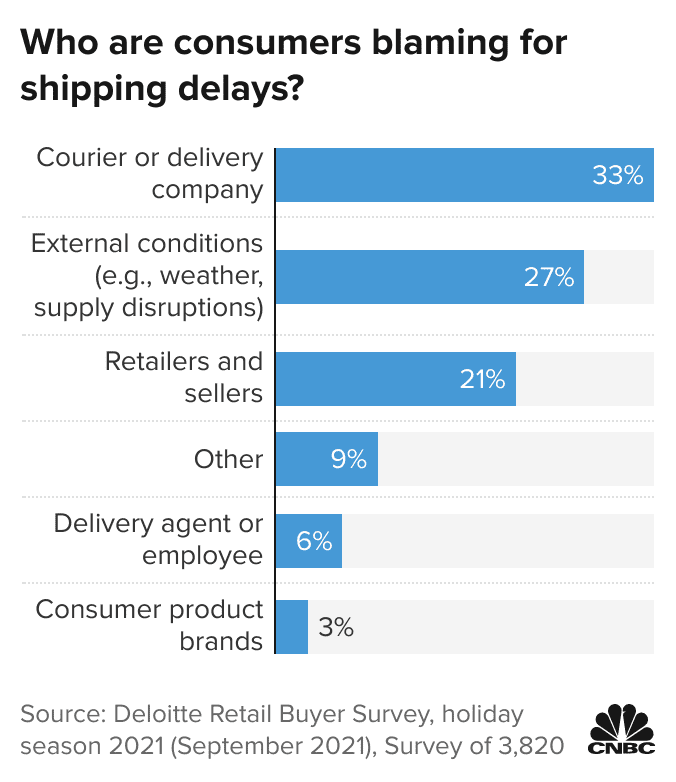
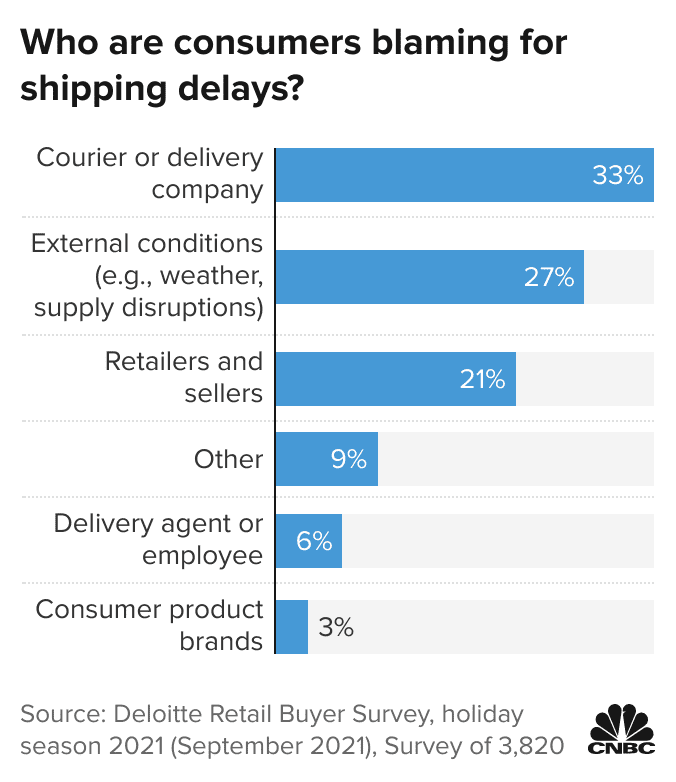
The impact of shipping delays
Even short shipping delays can ripple throughout your supply chain. For example, a late delivery of raw materials can disrupt the manufacturing process and delay the production of finished products. This, in turn, can lead to insufficient inventory levels and shortages of popular items during peak shipping season.
Shipping delays can also impact your customer loyalty. A survey from Voxware found that 65% of respondents will stop shopping with a brand after two to three late deliveries. So, if you want to maintain your customer’s loyalty, it’s important to do everything in your power to cultivate your brand’s supply chain resilience.
How to develop supply chain resilience
Supply chain resilience is the ability to quickly adapt and recover from unexpected events, no matter the cause. The following strategies could help you cultivate resilience in your supply chain, and minimize the impacts of shipping delays for your customers.
Track your data
To understand which parts of your supply chain are the most vulnerable to delays, you’ll need to gather data. Keep track of your key performance indicators (KPIs), such as the time that items spend in storage or the shipment times to and from different facilities.
You can gather this data in several ways, such as through trackers on shipments or warehouse management systems (WMS.) When you have the information in front of you, you’ll be able to identify any potential weak spots and plan adjustments for emergencies.
Move away from a “just in time” model
A “just in time” (JIT) supply chain strategy times deliveries so that they arrive just before you need them. This approach means that inventory doesn’t spend as much time stockpiled in warehouses, which can lower your storage costs. That said, a JIT model is vulnerable to supply chain disruptions since you won’t have as much spare inventory on hand.
To prevent the potential drawbacks of JIT, consider expanding your inventory to accommodate a small backup supply of materials or products, so you can continue to ship even when your suppliers experience delays.
Diversify suppliers
One way to avoid recent supply chain disruptions is to work with multiple suppliers in different parts of the world. For example, use both a domestic and international option. That way, if a storm or trade route blockage impacts one area, you still have a way to keep your supply chain operational without delays.
Invest in new technology
Take full advantage of technology to make your operations more efficient, like automated warehouse sorting and retrieving systems. When you can simplify the process of picking, organizing, and shipping items, you can get them on the road faster and minimize the potential downtime from a supply chain delay.
Up your customer service
While no one likes waiting for a package, some research indicates that good customer service can make up for late deliveries.
A 2021 survey from Mitto found that over 90% of respondents were more likely to have patience for shipping delays if they also received good customer service from the brand. In contrast, 55% of respondents reported canceling a delayed order if customer service was poor.
Strive for transparent and fast responses with your customer service so your customers stay in the loop and understand what to expect.
Work with a local transportation company
Lastly, if your business operations mainly concentrate in one region, such as New England, it may be to your best advantage to work with a locally based transportation company rather than a national organization.
If any regional shipping delays impact your area, a smaller local company will be able to devote more time and energy to handling them, rather than a national shipping company that must spread itself thinner to meet other customer’s needs. And when you can ship after a delay period, a local provider will also be able to get items to their end destinations faster than a company based in a location further away.
A New England trucking company you can trust
If you’re looking for a New England trucking company that can help you navigate through shipping delays, N&D Transportation is here to help.
We’ll work hard to help you meet your shipping goals and deadlines and find solutions to minimize the effects of shipping delays. Our North Smithfield Distribution warehouse is centrally located near major freeways, so we can get your items on the road as soon as possible.
Contact us today to learn how we can help your business grow.