Over 145,000 people work in the warehousing industry in the United States. According to the Bureau of Labor Statistics (BLS), warehouse workers may face a higher risk of injuries than employees in other industries. Which is why warehouse safety is so important. The warehousing and storage industries have an average injury rate of 4.8 per 100 workers, according to data from 2020. That’s much higher than the national average of 2.7 per 100 workers for all other private industries. So, it’s crucial that warehouse owners and managers take every precaution available to keep their employees safe.
To help you improve your current processes, the following warehouse safety improvement ideas could get you on the right track.
A warehouse safety checklist
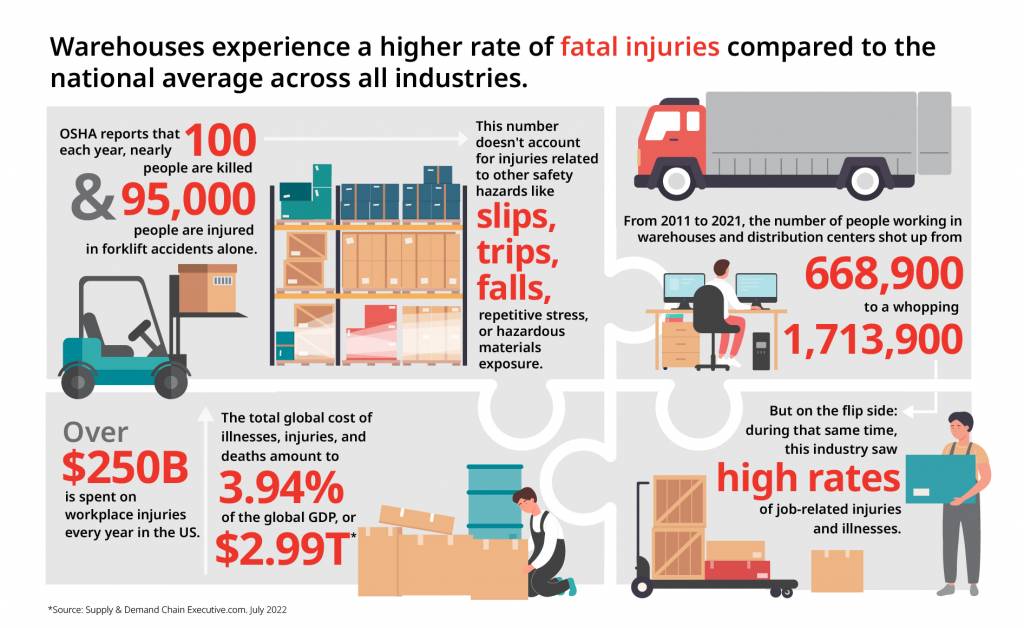
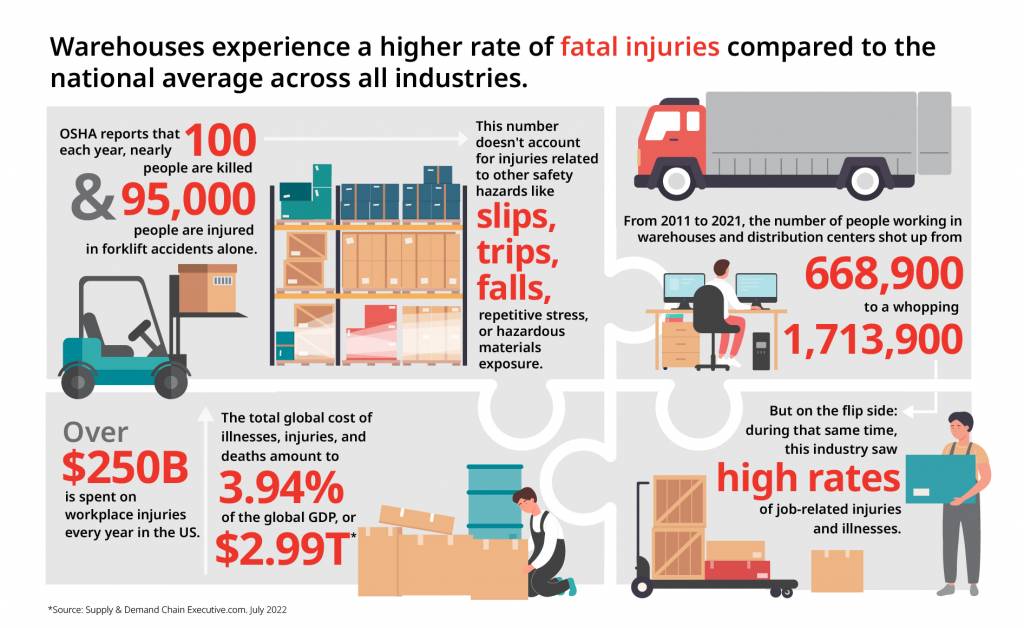
1. Provide proper training for forklifts
Around 100 workers are killed operating forklifts while another 95,000 are injured every year in the U.S. But the following tips could help your employees stay safe around this heavy machinery.
- Ensure employees have proper training: Only employees who are trained and certified should operate a forklift – and they should have training for the particular models used in your warehouse.
- Maintain clear visibility: Ensure that a forklift’s work area is clear from any potential obstructions and that the operator has enough room to maneuver it properly.
- Regularly inspect forklifts: Forklifts should ideally be inspected once per day to check controls and to spot any equipment damage.
2. Optimize your warehouse layout
Overexertion is one of the top contributing factors to injuries among workers, especially when lifting heavy palettes. Beyond providing your employees with proper warehouse safety training on lifting methods, you can also turn to the layout of your warehouse itself to minimize potential injuries. For instance, consider raising palettes that weigh 35 pounds or more at or near elbow height, so that employees can minimize the lifting distance.
3. Stack items carefully
Speaking of heavy palettes, improperly stacked items could quickly become dangerous on higher shelves. Therefore, it’s important that items should be stacked squarely and straight without overhanging edges. Subsequently, for added stability, try to keep heavier items toward the bottom of the pile, and consider an interlocking system when possible.
4. Make sure employees understand hazardous materials
If your facility handles hazardous materials, like chemicals, it’s important that employees understand the potential dangers that could arise from handling them.
Ways you could accomplish this include:
- Keeping accurate records: Maintain a Material Safety Data Sheet (MSD) of all the chemicals that workers could be exposed to at your facility.
- Provide a clean-up plan: Your MSD should ideally provide instructions on how to clean up spills, with properly labeled clean-up kits located at easy-to-reach locations.
- Provide personal protective equipment: Your facility should have adequate PPEs, like respiratory masks, for all employees in easy-to-access spots.
5. Conduct regular risk assessments
It’s important to conduct regular risk assessments for any new hazards in any warehouse, especially one that stores dangerous chemicals. Ideally, this should be done once per year before the peak season. A typical risk assessment for a warehouse should include:
- Documentation of all potential hazards and their control measures.
- Interviews with employees, for insight into daily operations.
- Consulting with safety experts for specialized advice in unique scenarios.
6. Secure charging stations
Equipment refueling stations can present a fire hazard. That can be true regardless of whether your warehouse equipment primarily runs on gasoline, propane, or another fuel source.
Therefore, to curb the potential risk, refueling stations should be located in well-ventilated areas and away from busier zones of the warehouse to prevent traffic jams. Additionally, precautions should also be taken to prevent open flames, sparks, or electrical arcs in the area, such as a ban on smoking for warehouse employees.
7. Secure electrical equipment
To prevent shocks or injuries resulting from electricity, the OHSA recommends that all equipment operating at 50 volts or more be “guarded” to protect staff. Guarding involves enclosing the live parts to ensure that people don’t come into contact with them. For example, placing the equipment in a room, vault, or elevated platform. A permanent screen can also do the job.
8. Provide proper railings
Slip and falls are one of the most common workplace injuries in the country. Therefore, to prevent falls, the OHSA recommends roping or blocking off any areas where an employee could fall more than four feet. Covers or guardrails should also be in place in stair openings, near equipment pits, or similar hazards like elevated walkways.
9. Follow a lockout and tagout procedure
When performing maintenance on equipment, it’s crucial to follow a “lockout/tagout” routine, to prevent employees from accidentally being electrocuted. Additionally, this means that the piece of equipment or machinery should be disconnected from its power source, and then isolated, so it can’t accidentally draw in power while it undergoes maintenance. The OHSA suggests using a lockout divide, which holds the equipment’s switch in the “off” position, for an added level of security.
10. Asses your emergency exits
Your warehouse should be equipped with clearly marked emergency exits. But it’s crucial to ensure that the exit route is well-lit and clear of any potential obstructions, like a forklift parked in front of the door. Furthermore, to ensure the exit routes stay unobstructed, properly train your employees in safety protocol.
A Rhode Island warehouse where safety is key
Warehouses are among the most potentially hazardous workplaces in the U.S. However you can keep your employees safe through proper warehouse safety training, changing your warehouse’s layout for ergonomic advantages, and regularly assessing your warehouse for potential risks.
If you need a New England warehouse you can trust, N&D Transportation is here to help. For instance, we prioritize safety in our daily operations, so you can store your items securely with us and avoid putting your own employees at risk. Learn more about fulfilling your storage needs with us via our contact page. Or, check out our blog for more tips on running and operating a warehouse smoothly.