Some people might use the terms “warehouse” and “distribution center” interchangeably. While the two can overlap in several ways, there’s actually a subtle difference between them. The difference between a warehouse and a distribution center can be simplified into a few main concepts.
In a nutshell, warehouses primarily hold goods until they’re needed for distribution. On the other hand, distribution centers handle the actual shipping and movement of products. Both can play a key role in an efficient supply chain — and some facilities offer the benefits of a warehouse and distribution center rolled into one.
Learn more about the differences between warehouses and distribution centers below, and discover why you need them in your supply chain.
What Is A Warehouse?
A warehouse is a type of storage facility designed to hold raw materials or manufactured products so that you don’t need to house them on-site.
Therefore, warehouses typically employ a racking system to maximize the amount of storage space they can fit into a single building. Furthermore, warehouse owners or operators may employ a warehouse management system to keep an accurate account of your inventory on hand.
What Is The Role of A Warehouse? Difference Between A Warehouse Role And Distribution Centers
Essentially, warehouses act as a middle point between manufacturers or suppliers and end consumers. The role of warehousing is to help ensure that products are available when and where they are needed and can help to mitigate the risk of supply chain disruptions by providing a buffer of inventory.
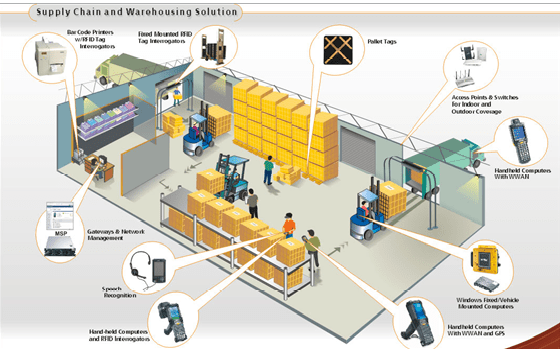
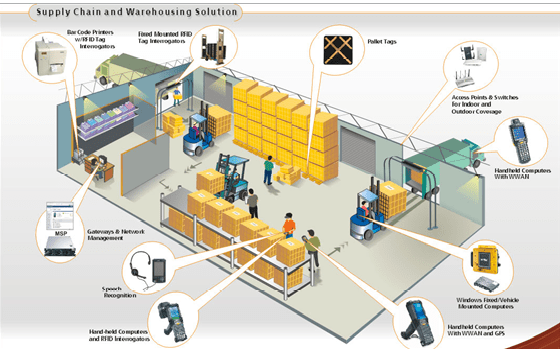
What Are The Benefits of A Warehouse?
Beyond expanding your storage capabilities, other benefits of warehousing include:
- Cost Savings: With a third-party warehouse, you’re not shouldering the overhead cost of operating the storage facility yourself.
- Increased security: A warehouse’s built-in security systems and staff can supervise your goods and keep them safe from theft.
- Scalability: If your storage needs suddenly change, all you need to do is lease more or less space from your third-party warehouse.
- Better inventory management: The facility’s warehouse management software can track and organize your goods, so you’re never left guessing about what you have on hand.
Additionally, different types of warehouses may offer specialized perks, such as climate control services to keep temperature-sensitive goods safe in certain locations. For example, a heated warehouse can keep liquids from freezing in the winter.
What Is A Distribution Center?
A distribution center is a centralized hub where products can be sorted and shipped out to their final destination — or, in the case of raw materials, to the next link in the supply chain. They’re sometimes called fulfillment centers.
However, unlike warehouses, these facilities focus more on the movement of products rather than their storage, making them ideal for keeping up in a fast-paced commerce environment.
Why Are Distribution Centers Important? Difference Between A Warehouse
Distribution centers perform the actual process of packing, labeling, and fulfilling deliveries. For instance, if you’ve ever received a package the day after you ordered it, it was likely processed at a local distribution center.
They’re often located near highways or major transportation hubs, so they can get your goods on the road as quickly as possible and ensure fast delivery times. Additionally, they can handle both inbound and outbound logistics services and assist in reverse logistics, should you need to process returns.
What Are The Advantages and Disadvantages of Distribution Centers?
Distribution centers offer many of the same advantages as warehouses, including better inventory management and a smaller overhead cost. As an example, you can save time and resources on shipping, as you won’t need to hire dedicated personnel to manage
Using a third-party source may come with some drawbacks, such as a loss of control over the shipping process. However, if you don’t want to handle the headache of processing orders in-house, a third-party partner could be the perfect solution for your logistic needs.
When Do You Need a Distribution Center vs. A Warehouse?
Now that you know the key differences between warehouses and distribution centers, which one do you need for your business? Well, that depends.
For instance, if you mainly need a safe place to store items offsite, especially for months or possibly years, a warehouse might be a better choice for your needs. You can be assured that your goods will remain safe and well looked after until you need them to ship out.
However, if you prioritize deliveries or need to move larger quantities of items fast, working with a third-party distribution center might help you streamline the fulfillment process. Furthermore, distribution centers can help you with other key aspects, such as packing and labeling deliveries or assisting with processing returns.
That being said, you don’t have to choose between one or the other. For instance, many third-party facilities combine the storage capabilities of a warehouse with the efficiency of a distribution center. Therefore, by working with a single provider, you don’t have to pick and choose what services you need — and you can keep costs down by outsourcing with one dedicated partner.
A Northeast Warehouse And Distribution Center for You
Looking for a Rhode Island-based warehouse or distribution center? N&D Transportation Company could have the solution you’re looking for.
At our 12-acre NorthSmithfield warehouse and distribution facility, we offer well-organized racked and heated warehouse storage space, which can keep your products secure for months or years. Additionally, when you’re ready to ship, we also offer distribution and fulfillment services. Thanks to our centralized location, we can get your goods on the road ASAP.
Additionally, if you need help getting your goods from point A to Point B, we can help you with truckload and less-than-truckload shipping services directly throughout New England.
Contact us today for more info on what we can do for your business.